Planning for Peak Supply Chain Amidst Global Disruptions
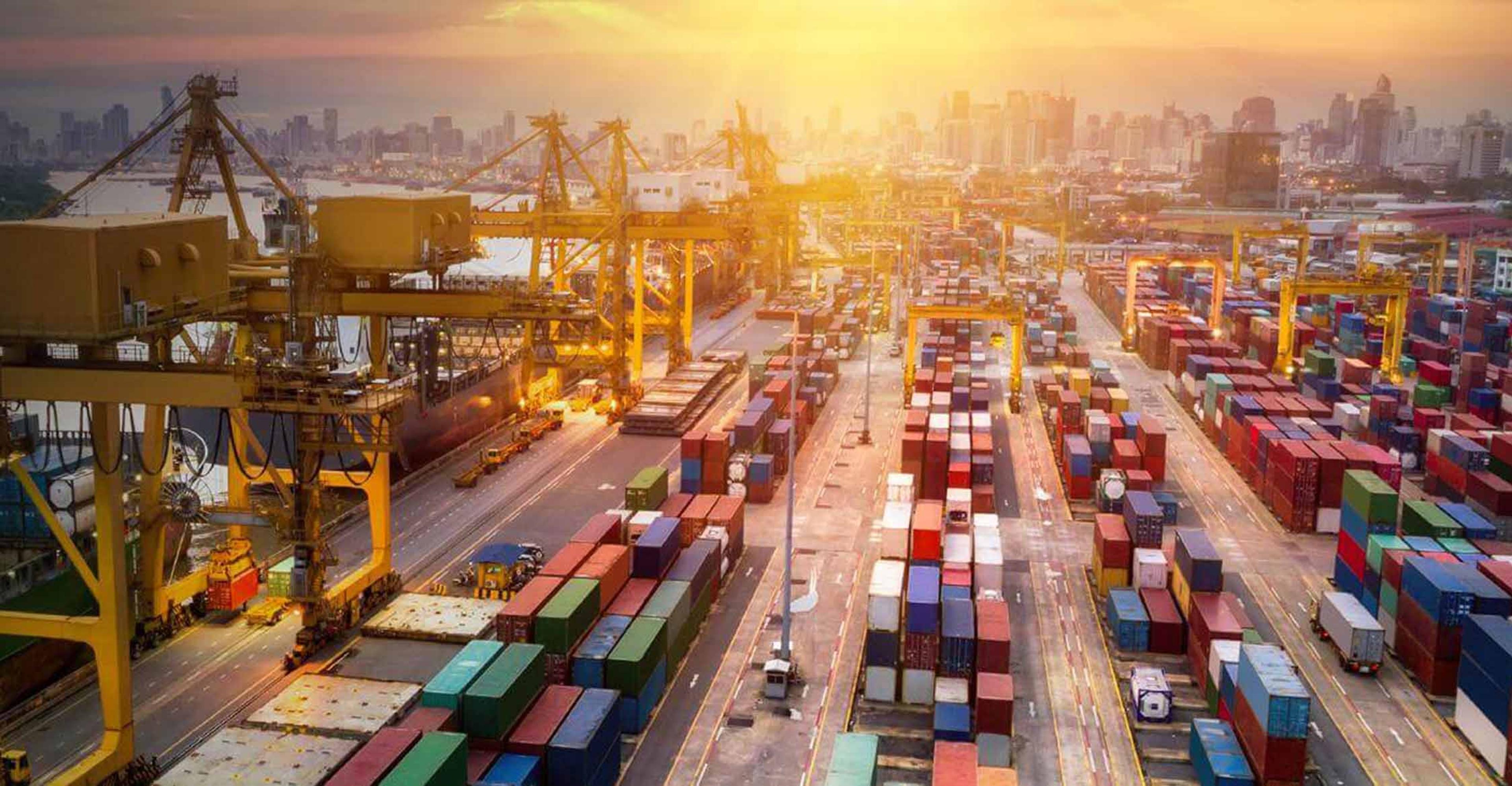
Planning for peak supply chain as a year-round endeavor
No matter the size and capacity of a business, navigating peak season can come with its challenges in today’s disrupted and constantly shifting supply chain environment. Tried-and-true methods are no longer enough to guarantee success when hit with high demand. Current shifting trends are an indication that it is never too early to begin planning for peak supply chain season.
The uneven responses to supply chain challenges make it nearly impossible to forecast demand shifts accurately anymore. Slower supply chains and stock shortages may lead to rising demand, such as the toilet paper shortage at the beginning of the pandemic. However, the opposite can also be true as we are seeing today with consumers spending less money in an inflationary environment.
Being aware of every stage in the supply chain, its challenges, and optimization opportunities is key to success with today’s logistics challenges. Preparing your business throughout the year to weather ups and downs in the market will provide a competitive advantage. With conflicts abroad, impacts of weather variations, shortages of labor, rising fuel prices, increasing consumer expectations, and the unpredictability of the supply chain, being prepared no matter the season can help prevent many headaches later.
Manufacturing logistics management
Virtually every industry has experienced ripple effects as supply chain disruptions impact manufacturing and production. 94% of Fortune 1000 companies are experiencing supply chain-related disruptions and 75% are facing negative business impacts as a result. Raw material availability may be an issue depending on a myriad of factors. Production facilities are facing considerable backlog due to global conditions, labor shortages, and high demand.
The good news is that this is a universal issue. In many industrial inventory cases, factories have most of their needed parts on hand but can’t move forward with production because of one vital missing piece. John Deere has $1.6 billion of “work in process” inventory, up from $967 million one year ago. However, once the missing parts show up the partially finished products will eventually be sold.
When planning for peak season, be considerate of where manufacturing is being sourced, the availability of raw materials, lead times, and geography for customs clearance and possible import/export fees. In times of constraint there is an opportunity to innovate. Explore alternative raw materials, consider working with local manufacturers, and think about where your buyers are geographically. Historically, both retailers and manufacturers have minimized their supply chain risks for future events that could cause trouble. But in today’s world, disruptions occur with little to no warning.
Ocean freight transportation amidst port congestion
As China lifts its lockdowns and reopens the Port of Shanghai, the United States can expect some degree of congestion from ocean freight. Some bottlenecks have already formed due to inland transportation, labor restraints, and the availability of raw materials. Barring no further shutdowns or restrictions, experts expect U.S. ports to return to normal capacity within a couple of weeks’ time.
While volumes from Asia were down during the lockdown, other ports have picked up pace as traffic was diverted. West coast ports of the U.S. will certainly see some backlog, but because smaller ports were able to relieve some pressure it won’t be as bad as originally expected. The lockdowns provided some breathing room to work through existing backlogs and improve operations in China.
Drayage and intermodal peak period
While intermodal can be somewhat slower than over-the-road (OTR) shipments, the average variability is about one to two days. The lower cost of intermodal when compared to trucking often offsets the longer transit time. Another advantage of intermodal shipments is the high visibility – they often pass through checkpoints that provide tracking data. Intermodal has made large strides in improving service through the enhancements of facilities, tracks, and technology. As truck capacity has become constrained, many companies have turned to intermodal services. One train can carry the loads of approximately 280 trucks and rail is about four times as fuel efficient as trucking.
To boost intermodal service, first consider the distance the shipment will travel. Intermodal tends to work best with routes of about 700 miles or more. Another consideration is the load itself. Shipments of raw materials are perfect for intermodal, as they can afford longer transit times and don’t need to be sold off right away. Aligning shipments with rail schedules will provide an even stronger supply chain. Experts advise shippers to keep in mind potential weight-dimension imbalances that could affect rail-to-road compliance.
Warehouse and distribution customer expectations
In years past, fulfillment strategies focused on maintaining the status quo and relying on outdated systems when peak season arrives. Today’s supply chain technology provides users with a large amount of data to make hiring, inventory, and shipping capacity decisions. There are three peak season fulfillment strategies that can be used in a closed circuit to balance warehouse management for optimal results: robust replenishment, keeping employees productive, and guaranteeing customer service.
To build such strategies, there are several concepts to focus on to reach peak warehousing management. Lean inventory strategies may fall short during peak season fulfillment, despite being an excellent strategy at other times of the year. Warehouse should be running around the clock, with ample time for all workers to rest or take breaks. Providing amenities like on-site cafeterias or food delivery will go a long way with team members working long hours. Be sure to implement end-to-end visibility tools by tracking deliveries and delivery schedules, benchmark systems to identify maximum throughput, and re-slot peak season item areas. Take advantage of omnichannel inventory, automation, and other trending ecommerce solutions.
Labor challenges among increased demand
Even with recent wage increases across the warehouse and carrier industry, companies are still struggling to hire front-line workers. Brands began to stockpile inventory and plan for longer fulfillment cycles, while many others expanded their distribution centers. Heavy investments were made with the intention to secure operations in the long-term. Supply chain managers had to pivot away from a “Just in Time” (JIT) order fulfillment approach to a “Just in Case” (JIC) supply chain strategy.
Transitioning to a JIC strategy does not consist of taking best guess at inventory needs or buying out suppliers at every turn. Companies should be relying heavily on data, including e-commerce data, logistics data, and inventory performance data, to adjust inventory management and optimize lead times. Having increased data visibility will enable brands to make decisions to deliver optimal results for both their customers and their bottom line.
Buying behavior around the customer experience
The United States government reported that consumer prices have climbed a whopping 8.6% Jan-May of this year. Various global factors are driving up prices in every market, including strong consumer demand, too few goods, and service-sector pressures. As inflation takes hold and prices go up, conditions for the consumer have deteriorated in a short timeframe. Americans are tightening their wallets as interest rates rise, while at the same time spending money on in-person experiences rather than goods. This quick change in buying behavior has left retail stockpiles at a record high.
Selling off these mountains of goods will shape growth rates in the U.S. economy. Discounts required to clear warehouse space could offer American shoppers some relief but will do little to reduce the record high inflation rate. The global economy is suffering from a timing mismatch and a demand mismatch between goods available and goods sold. Now is an important time to pay attention to where your customers are spending money and how you can adjust your offerings to current buying behavior.
A trustworthy 3PL solutions provider
Among all the decisions involved when it comes to supply chain management, partnering with a trusted third-party logistics provider is essential for ensuring profitability. At ITS Logistics, our customers can rely on high level service, the latest technology, and creative solutions all while working to deeply understand your business needs. Supply chain experts predict that the problems in the supply chain caused by the pandemic could take another two years to fix at minimum. By working with a logistics partner, companies can focus on their core business even during times of seasonal demand.