News + Resources
Blog | Technology
Freight Fraud in 2025: Insight from the Frontlines

Filter by
All Resources
All Categories
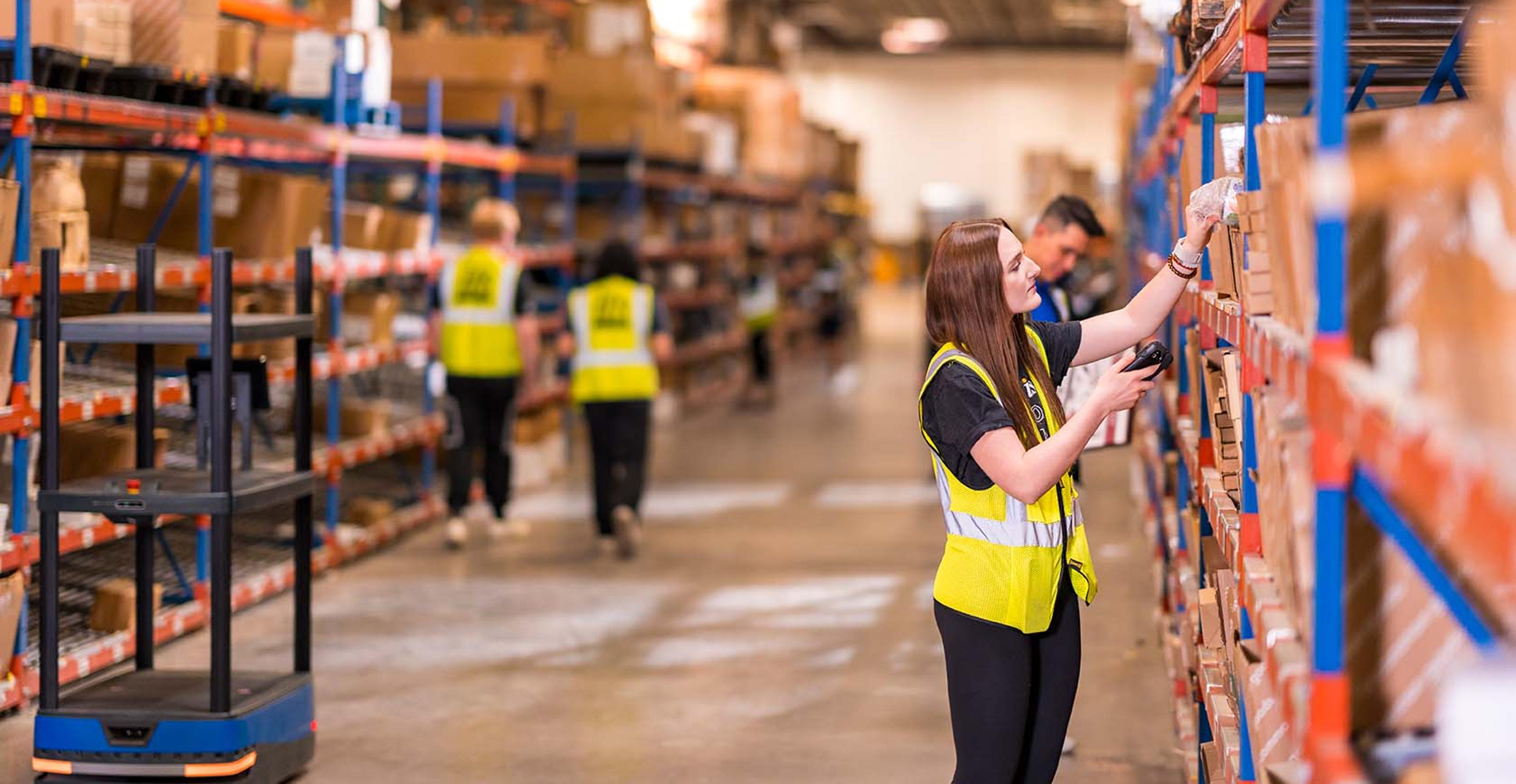
IN THE NEWS: Deep Inside US Economy, More Sticker Prices Start Going Up Due to Tariffs, and Inventory is Headed Down
Blog | Company News

ITS Logistics Named to Inbound Logistics' 2025 75 Green Supply Chain Partners List for Advancing Sustainable Supply Chain Practices
Press Release | Sustainability
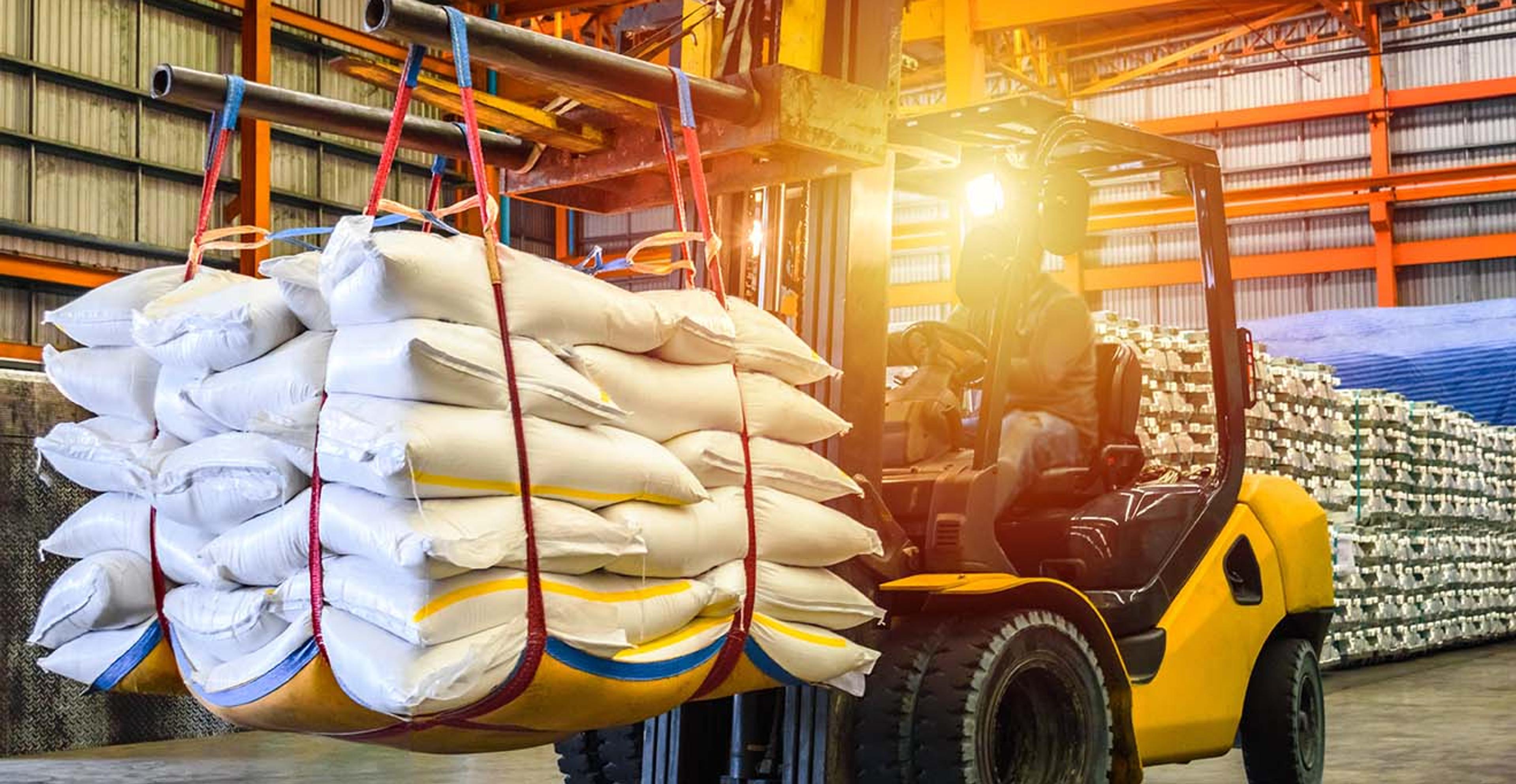
ITS Logistics Launches National Food & Beverage Logistics Hubs to Advance US Supply Chain Performance
Press Release
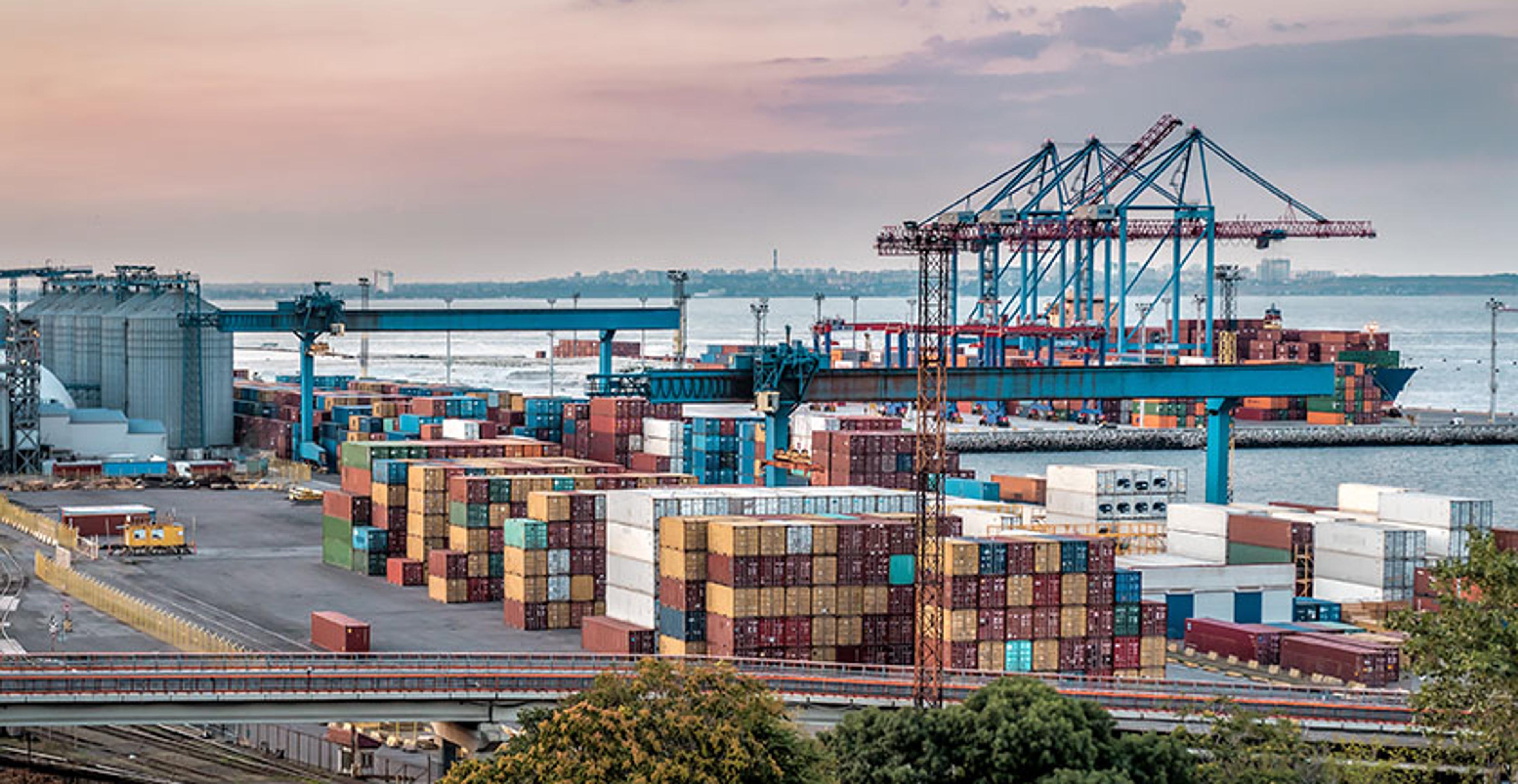
ITS Logistics June Port Rail Ramp Index: Trans-Shipment Delays in Asia Signal Impending US Import Surge, Spurring Early Retail Peak
Port + Rail Index | US Port/Rail Ramp Freight Index
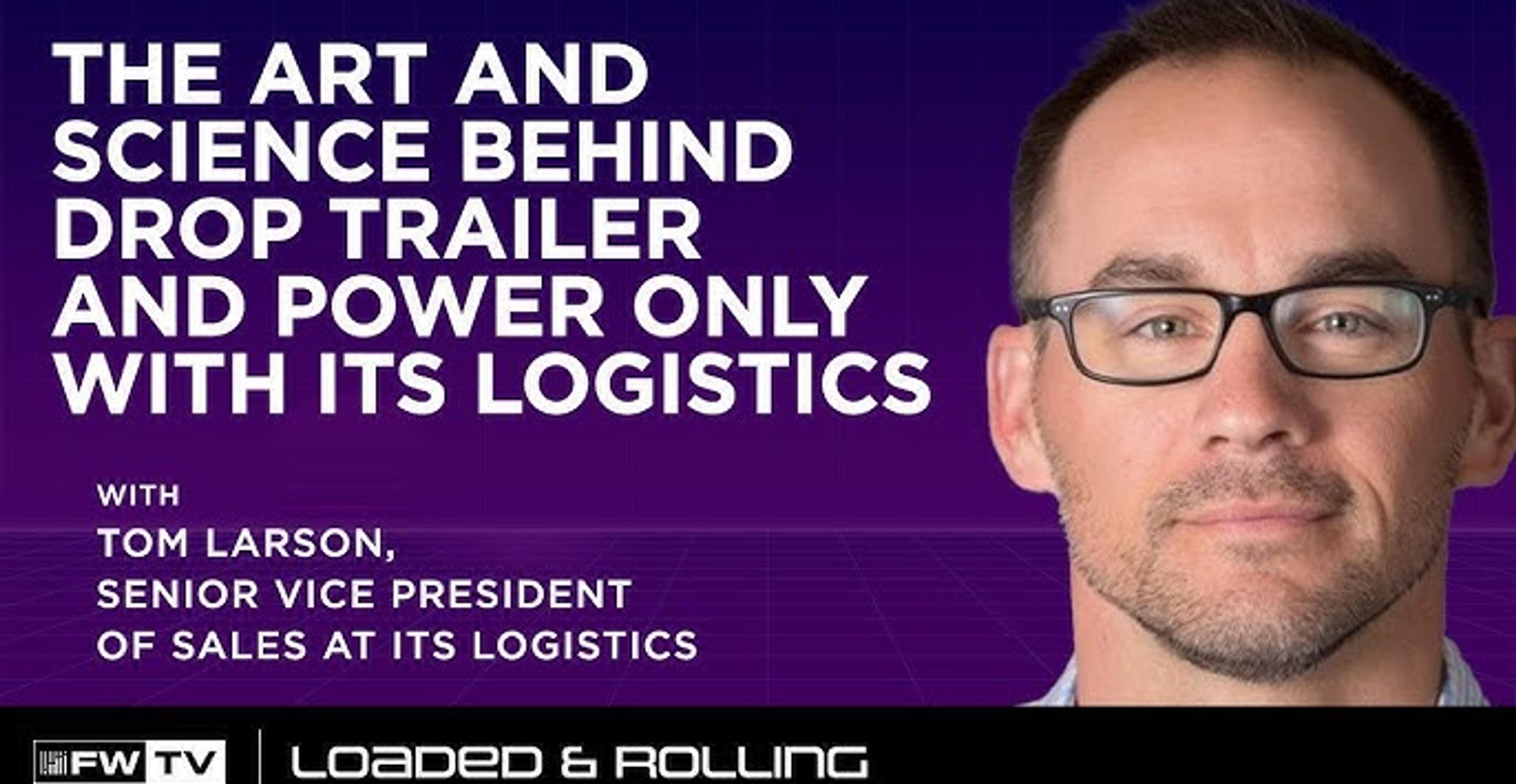
IN THE NEWS: The Art and Science Behind Drop Trailer and Power Only with ITS Logistics | Loaded and Rolling
Blog | Company News
…