News + Resources
Port + Rail Index | US Port/Rail Ramp Freight Index
ITS Logistics July Port Rail Ramp Index: Stable Port Operations Mask Uncertainty Over Remaining 2025 Shipping Activity

Filter by
All Resources
All Categories
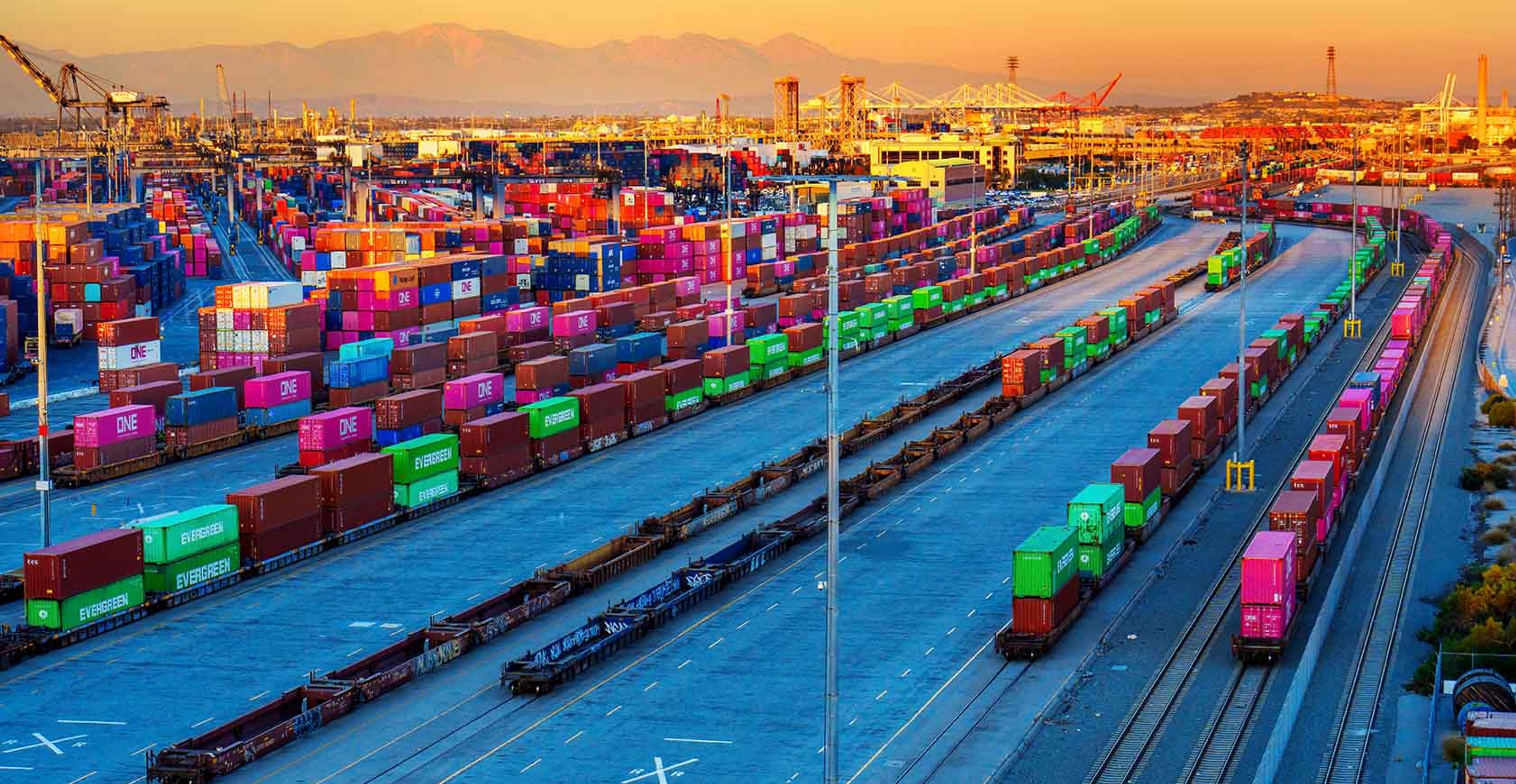
ITS Logistics July Port Rail Ramp Index: Stable Port Operations Mask Uncertainty Over Remaining 2025 Shipping Activity
Port + Rail Index | US Port/Rail Ramp Freight Index
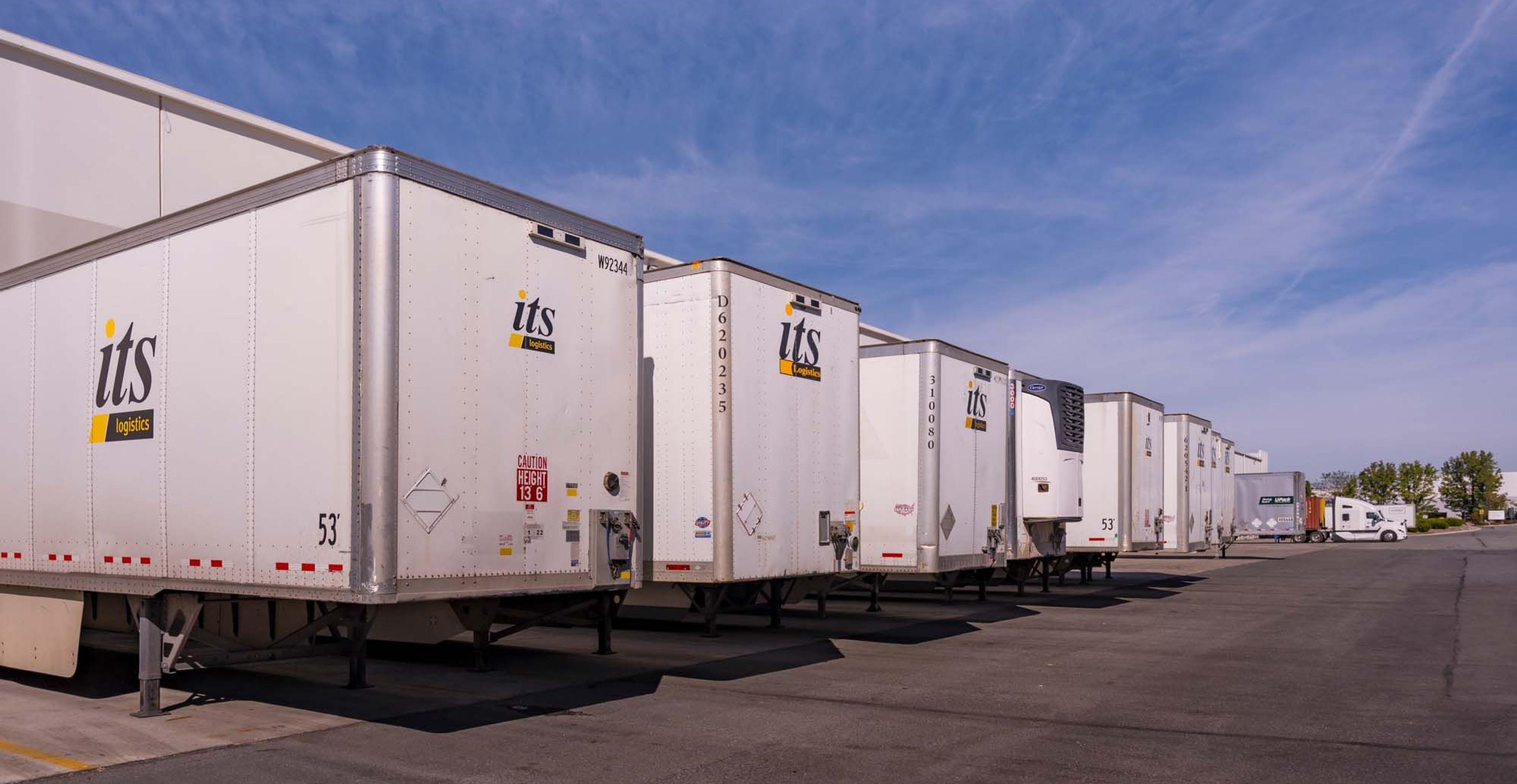
IN THE NEWS: In Middle of Trump’s Trade War, Importers Hold More Cash and Move Inventory off the Books
Blog | Company News
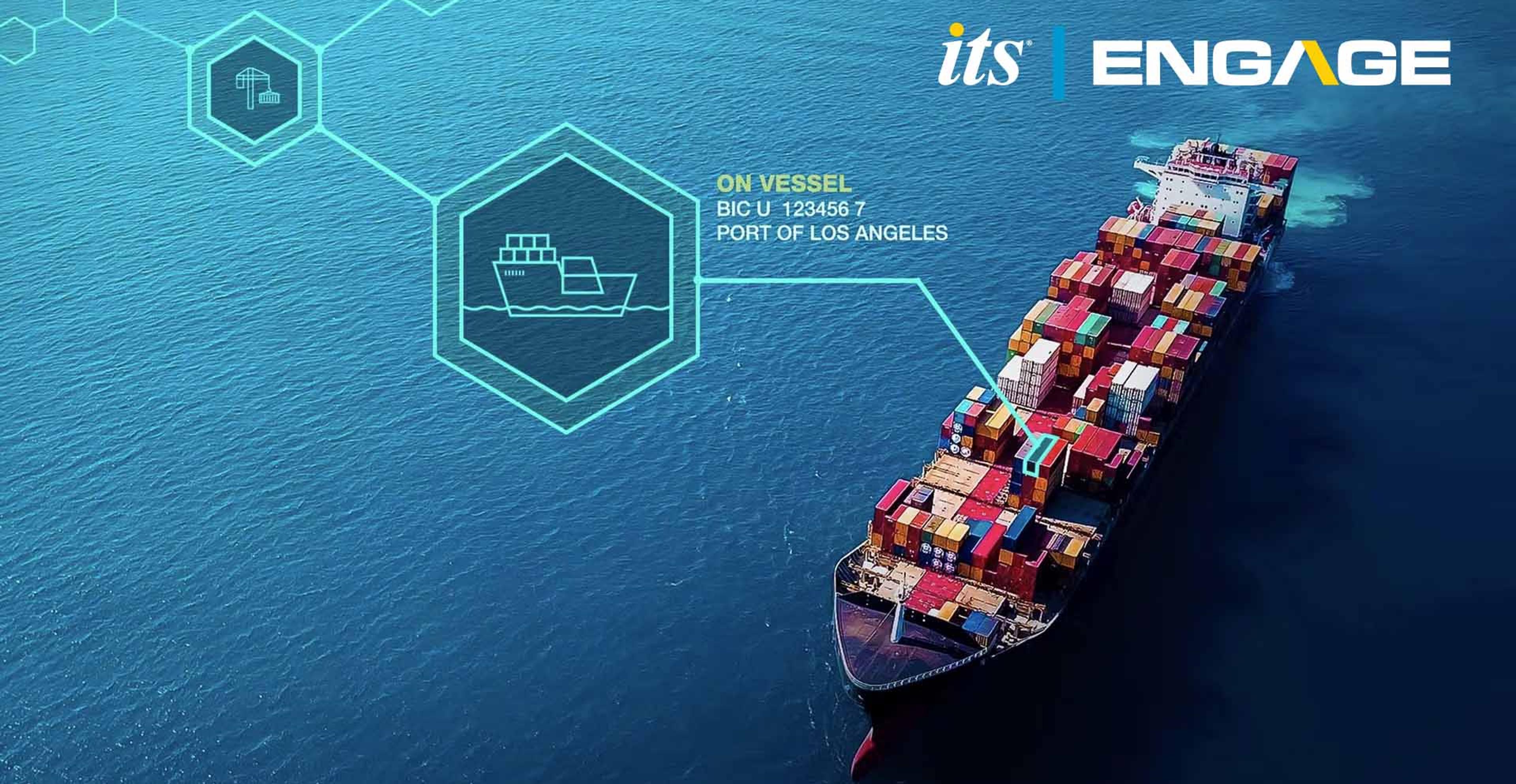
ITS Logistics Announces ITS Engage: A Centralized Ecosystem for Shippers, Carriers, and Supply Chain Partners
Press Release | Technology
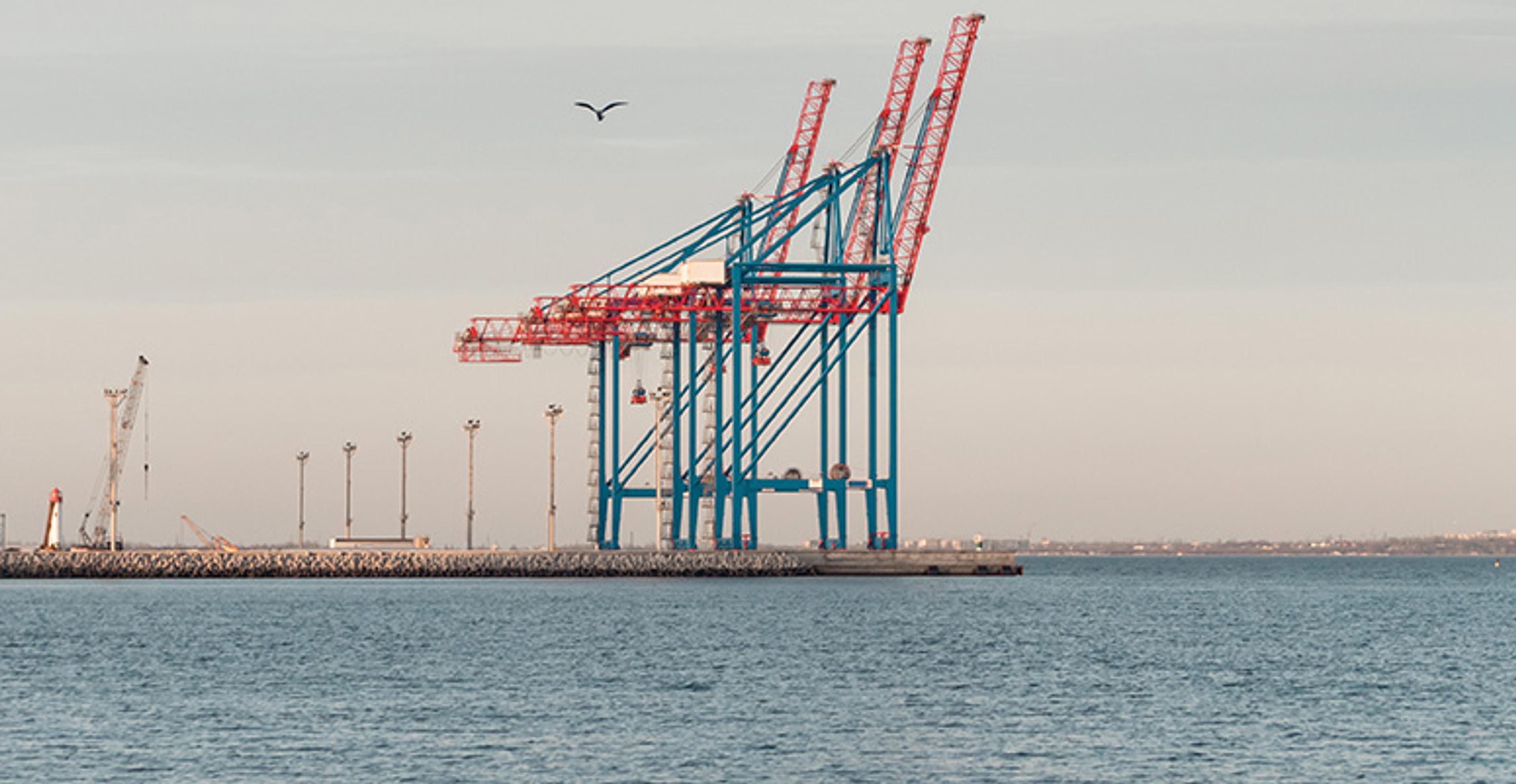
ITS Logistics June Supply Chain Report: Inventory Costs Increase as Port Container Volumes Sink to COVID-Era Lows
Market Update | Market Update
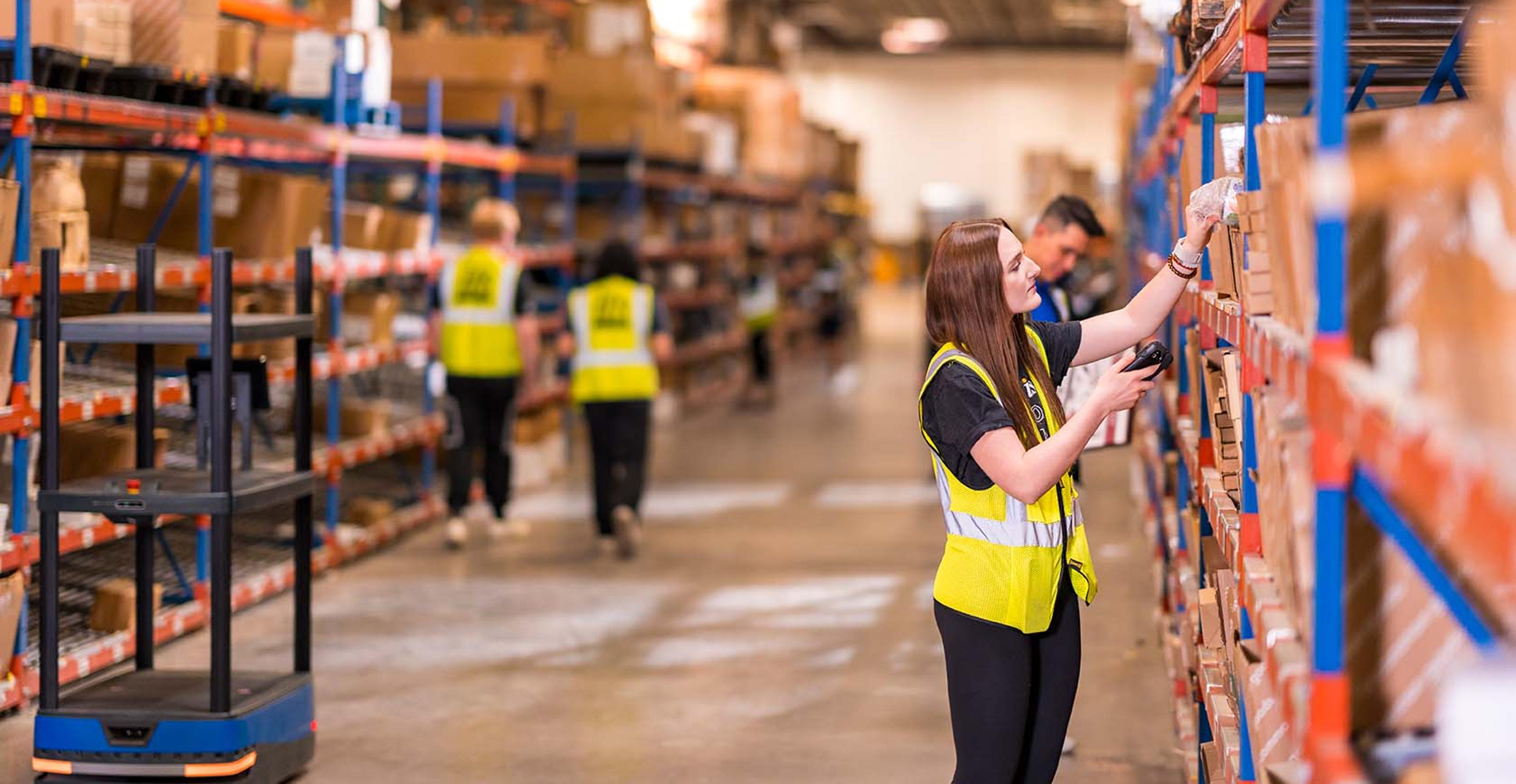
IN THE NEWS: Deep Inside US Economy, More Sticker Prices Start Going Up Due to Tariffs, and Inventory is Headed Down
Blog | Company News

ITS Logistics Named to Inbound Logistics' 2025 75 Green Supply Chain Partners List for Advancing Sustainable Supply Chain Practices
Press Release | Sustainability
…